The Essential Role of Tank Welding Assessment in Ensuring Structural Stability and Security Conformity in Industrial Applications
In the realm of commercial applications, storage tank welding inspection arises as a critical element in safeguarding structural honesty and ensuring compliance with safety and security regulations. Using a combination of methods such as visual analyses and advanced testing methods, these inspections offer to identify and mitigate possible imperfections prior to they escalate into considerable risks.
Importance of Storage Tank Welding Examination
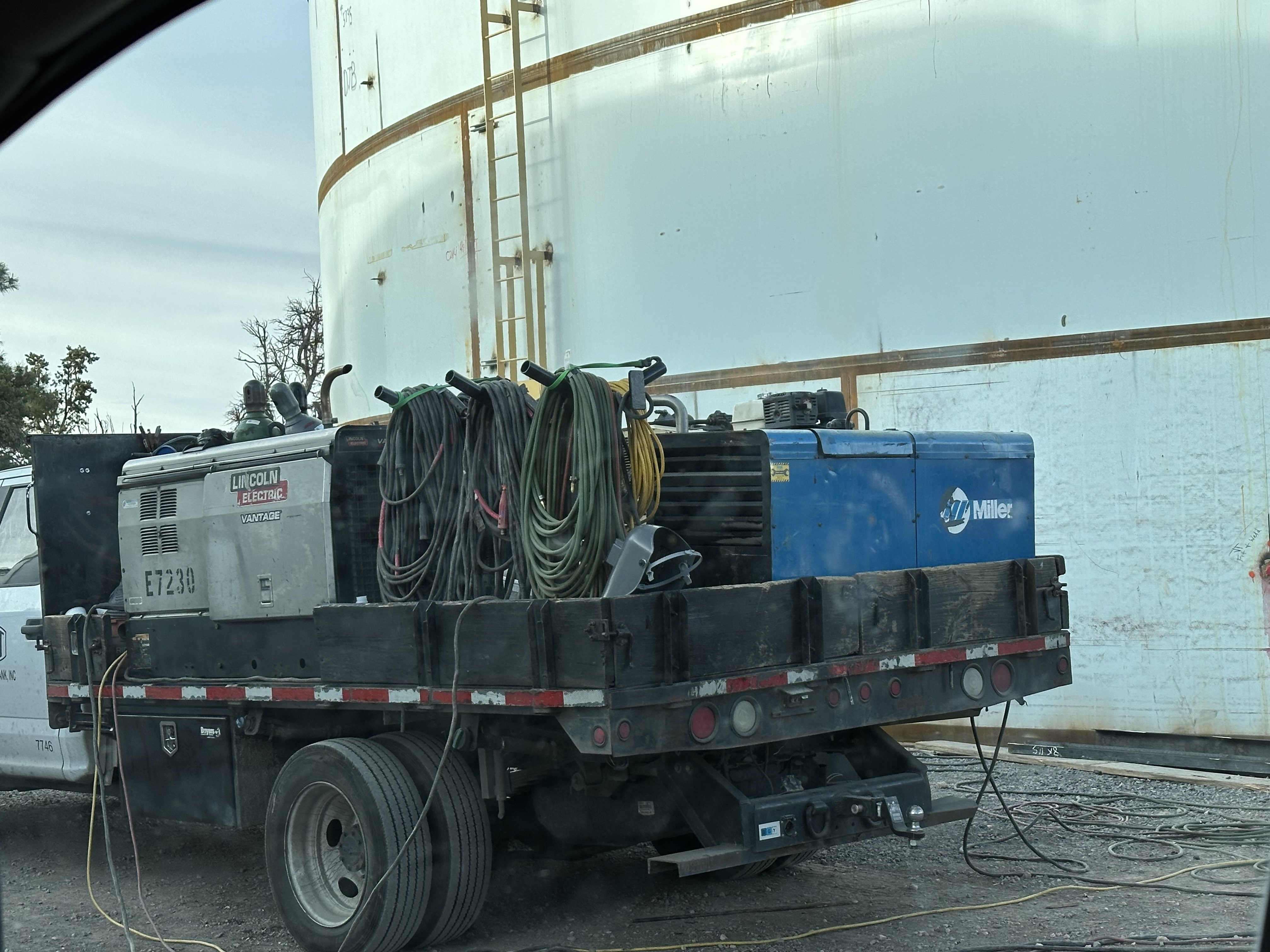
Ensuring conformity with market requirements and guidelines is another considerable aspect of storage tank welding examination. Regulative bodies mandate stringent standards for the construction and maintenance of tank, and extensive examinations help companies stick to these needs. Non-compliance can lead to severe fines, consisting of fines and shutdowns, additionally highlighting the need for extensive examination methods.
Moreover, storage tank welding examination plays a critical duty in keeping operational performance. Regular evaluations can identify prospective issues before they intensify, assisting in timely fixings and minimizing downtime. This positive strategy not just enhances security however additionally contributes to set you back financial savings in the long run. In summary, the significance of tank welding inspection depends on its capacity to safeguard public health, shield the atmosphere, and make certain compliance with regulatory frameworks.
Trick Inspection Methods
Effective tank welding assessment depends on a selection of essential methods that make sure detailed assessment of weld top quality and structural honesty. Amongst the most widespread strategies are visual inspection, ultrasonic screening, radiographic screening, and magnetic bit testing - Tank Welding Inspection. Each technique provides one-of-a-kind benefits in analyzing different aspects of the weld
Visual evaluation works as the initial line of protection, allowing inspectors to recognize surface area defects, abnormalities, or incongruities in the weld bead. Ultrasonic testing employs high-frequency audio waves to identify interior flaws, such as cracks or gaps, offering an extensive analysis of weld honesty. This technique is especially effective in identifying issues that might not show up on the surface.
Radiographic testing uses X-rays or gamma rays to create pictures of the welds, exposing interior gaps and offering an irreversible record for future recommendation. This technique is very reliable for vital applications where the danger of failure should be decreased.
Last but not least, magnetic fragment testing is employed to determine surface and near-surface flaws in ferromagnetic products. By using electromagnetic fields and fine iron bits, assessors can identify discontinuities that might jeopardize the structural integrity of the tank. With each other, these methods form a robust structure for making sure top quality welds in industrial applications.
Conformity With Safety And Security Standards
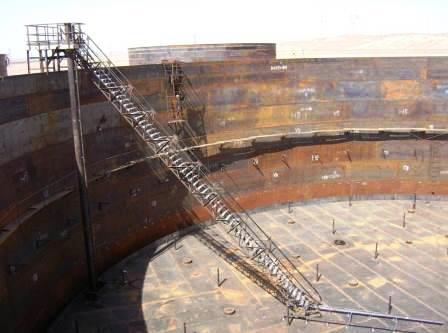
Routine evaluations play a pivotal function in guaranteeing conformity by recognizing prospective failures or variances from prescribed criteria. Inspectors are educated to assess weld high quality, validate product requirements, and evaluate the overall architectural integrity of tanks. Their proficiency is important in making certain that welding processes fulfill the called for safety standards.
Additionally, conformity with safety and security criteria not just shields employees yet additionally safeguards the atmosphere from prospective dangers such as leakages or catastrophic failings. Organizations that focus on security compliance are much better placed to alleviate risks, boost operational efficiency, and cultivate a society of security within their labor force. In recap, preserving rigorous compliance with safety and security standards is vital for the effective operation of tank welding tasks in industrial settings.
Advantages of Normal Examinations
Regular evaluations are essential to maintaining the architectural stability and security of bonded tanks. These evaluations provide an organized approach to identifying possible defects or weaknesses in the hop over to these guys welds, guaranteeing that any kind of concerns are addressed before they rise right into significant failings. By conducting normal assessments, companies can spot corrosion, fatigue, and other types of deterioration that may compromise storage tank performance.
Additionally, consistent evaluations add to compliance with sector policies and criteria. Sticking to these standards not just reduces lawful dangers yet likewise improves the organization's online reputation for safety and integrity. Normal inspections promote an aggressive safety society, encouraging employees to acknowledge and learn the facts here now focus on the importance of tools integrity.
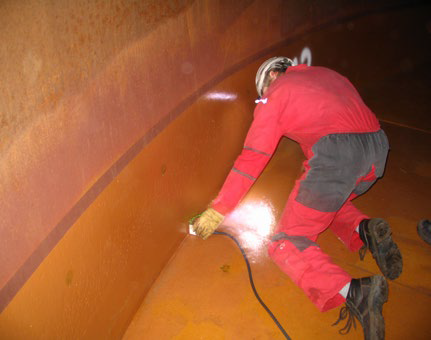
Situation Research Studies and Real-World Applications
Case researches and real-world applications illustrate the substantial effect of effective storage tank welding assessment techniques. Complying with the implementation of extensive welding examination methods, including visual and ultrasonic screening, the center identified vital imperfections in weld joints that might have led to catastrophic failures.
In a similar way, a water therapy plant carried out an extensive inspection program for its container welding procedures - Tank Welding Inspection. By including non-destructive screening approaches, the plant was able to detect early signs of deterioration and tiredness in weld joints. This timely treatment prolonged the life expectancy of the storage tanks image source and made sure compliance with security laws, hence safeguarding public wellness
These study emphasize the relevance of normal and systematic tank welding inspections. By prioritizing these methods, sectors can minimize threats, boost structural stability, and make sure conformity with security criteria, inevitably bring about improved functional performance and lowered responsibilities.

Conclusion
In final thought, container welding evaluation is a vital part of keeping architectural stability and safety and security in industrial applications. Using different assessment methods makes sure very early detection of potential problems, consequently protecting against disastrous failings.